Industrial remote monitoring involves tracking and analyzing near-real-time data from machines and equipment without needing to physically be present at their location. It allows operators to remotely monitor various performance metrics such as leaks, maintenance needs, vibration levels, emissions, data readings, pressure, voltage, and other potential hazards.
Integrating remote monitoring systems into a cloud-based software platform allows industrial facilities to gain critical visibility into their operations. They receive alerts for any anomalies that occur, can automatically initiate service tickets, and take proactive measures to prevent downtime.
In this article, we will delve into the world of industrial remote monitoring, exploring its business benefits, common use cases, and a basic understanding of how this solution works to revolutionize industrial operations.
Part One: The 3 Big Players in Industrial Remote Monitoring with IoT
With applications in nearly all major industries, you can expect to see countless types of industrial remote monitoring. However, regardless of your industry, three primary industrial IoT remote monitoring solutions consistently emerge as key players.
Conditions-based alerts: This involves real-time monitoring of equipment and systems to swiftly detect any deviations from normal operating conditions. This ensures timely notifications to your inbox or cellphone and allows for immediate intervention before small issues become massive events.
Predictive maintenance: This impressive ability often takes center stage by utilizing advanced data analysis and machine learning algorithms to forecast potential failures. By identifying issues before they occur, proactive maintenance can be implemented, effectively preventing unexpected downtime and lowering maintenance costs.
Automated processes: This intervention capitalizes on remote monitoring capabilities to optimize and streamline production operations. By leveraging this technology, industries can enhance efficiency and productivity by automating various aspects of their manufacturing workflows.
-1689225381.png)
Part Two: The 5 Main Business Benefits of Implementing Industrial Remote Monitoring Solutions
What’s more important, increased revenue or cost savings? Fortunately, with the right industrial remote monitoring solution in place—one that can flex and scale with your business’s needs—both, and more, are possible.
Benefit 1: Positive ROI
There are two sides to consider when evaluating the ROI of a solution like industrial remote monitoring. The first one is obvious: How will this solution increase revenue for my business? The second is often forgotten, but no less important: How much am I currently spending unnecessarily because I don’t have this solution? You’ll see just how great the ROI of remote monitoring is in the benefits below.
In summary, industrial remote monitoring maximizes on ROI by:
Lowering your operating costs
Keeping you compliant with regulations and avoiding hefty fines
Preventing unnecessary equipment downtime and lost production
Allowing you to scale without needing to add staff
Benefit 2: Optimize Performance & Quality
Industrial remote monitoring boosts performance by both helping you improve product quality and improving operational efficiency. Nothing can stop you if you can create a better product more efficiently.
By monitoring all aspects of production that affect quality—such as temperature, speed, vibration, flow, electrical connect, and infinitely more—your operators will know the second something happens that could infringe on quality. And the great thing about IoT-powered remote monitoring is you can visualize and control those processes from anywhere.
Additionally, your remote monitoring sensors will pick up a huge amount of near-real-time data that will be sent to the cloud to be analyzed. This data, when combined with machine learning algorithms, can lead to insights that help your operations become even more effective and efficient, such as eliminating unnecessary equipment downtime due to both breakdowns and suboptimal maintenance.
Here’s how industrial remote monitoring enables effective and efficient performance:
Predict failures in your processes and perform preventive maintenance
Identify the root causes of production issues, from failures to slowdowns
Proactively maintain equipment before they break down
Benefit 3: Stay Compliant with Regulatory Requirements
There are two sides to regulatory compliance. On one side, there are industries that require constant proof of compliance to make sure companies are following the law. Industrial remote monitoring helps with this by providing an accurate source of consistent data flowing from equipment sensors to the cloud center.
On the other side, there are the fines that companies face when found uncompliant, such as those faced by spilling waste or wastewater into the environment. Conditions-based alerts that monitor even slight changes in the process help companies respond faster to incidents and prevent the kind of massive events that lead to hundreds of thousands, or even millions, of dollars in fines.
Avoid problems with regulatory institutions with industrial remote monitoring by:
Proving compliance through a constant stream of data in cloud-based logs on your equipment and processes.
Receiving conditions-based alerts as soon as an incident is about to occur or occurs.
Through heightened visibility, knowing exactly what needs to be fixed to prevent said events
Benefit 4: Prevent Unnecessary Downtime
Downtime has several detrimental consequences, including potential revenue loss, higher expenses for unplanned repairs, and a decrease in client trust resulting from missed deadlines.
Intelligent maintenance practices improve equipment health and enable failure prediction, significantly reducing unnecessary downtime. While preventative services are scheduled at regular intervals based on average usage, users who exceed this average face a higher risk of wear-related failures. By utilizing IoT, organizations can gain insights into usage rates, wear rates, and error codes, facilitating a shift from time-based to condition-based maintenance. This transition ensures that work is performed when necessary, leading to reduced downtimes.
Another major cause of downtime is massive events that completely halt or at least hamper production. How much revenue are you losing for each hour or day of downtime while you fix equipment and clean up messes? Prevent these massive events from happening and see production running smoothly with continuous, near-real-time remote monitoring and alerts that will actually be heard.
Keep equipment and processes up and running as much as possible with industrial remote monitoring by:
Performing effective proactive maintenance based on near-real-time monitoring, rapid diagnostics, machine learning-informed predictive maintenance and automatic recalibrations.
Automatically triggering work orders for needed maintenance.
Receiving alerts to your computer and phone the moment an incident occurs so you can prevent massive failure.
Benefit 5: Lower Cost of Operations
It’s much more expensive to fix equipment after massive failure than it is to conduct routine maintenance. As described above, IoT-powered remote monitoring lets you do just that.
It’s time-consuming for operations to manually try and figure out what went wrong with equipment in order to fix it. The right monitoring solution can pinpoint exactly what needs to be fixed, letting your team fix it efficiently the first time they go out.
Downtime is expensive.
Regulatory noncompliance fines are very expensive.
Manual equipment inspections are expensive.
Industrial remote monitoring eases or prevents the financial burden of all of that. When combined with your optimized production, you can clearly see how the ROI of remote monitoring with IoT pays for itself.
-1689225350.png)
Part Three: A Few of the Most Common Use Cases of Industrial Remote Monitoring
Here are some of the industries that can benefit the most from remote monitoring with IoT.
Wastewater Treatment Plant Remote Monitoring
Monitor tank levels to prevent spills and leaks.
Learn about spills or equipment failure just in time by receiving conditions-based alerts the moment something happens, sent via SMS and email to the right people.
Avoid heavy non-compliance fines by receiving notifications before sensor readings become critical.
Manufacturing Industries
Real-time monitoring reduces equipment downtime
Cut maintenance costs through remote asset visibility and predictive maintenance.
Improve worker safety by implementing wireless systems in potentially dangerous work environments.
Oil, Gas & Energy Monitoring
Extend OEM equipment lifespan by monitoring for wear & tear trends
Detect anomalies for upstream operations effectively and at scale
Detect hazardous gases before major events occur
Inventory and Industrial Asset Monitoring
Monitor valuable fixed and moving assets with IoT and management software
Conduct inspections remotely that replace or reduce on-site, manual visits
Use Radio Frequency Identification (RFID) tags to transfer information about assets and inventory, including location data, truck speed, fuel consumption, etc.
Farm Asset Management
Automate maintenance workflows to keep your equipment in operation, minimizing your need to halt production
Save your workers valuable time on reactively repairing equipment with a predictive maintenance program.
Extend farm equipment and asset lifecycle
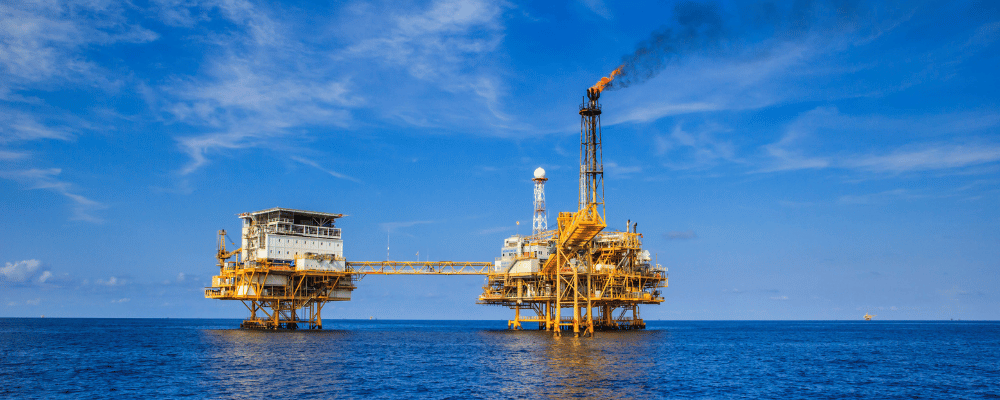
Part Four: How Does Industrial Remote Monitoring with IoT Work?
In a complex remote monitoring solution, these steps—collecting, communicating, analyzing, visualizing, and acting on data—are not strictly linear. They often occur in a continuous loop, with real-time feedback and automation enabling constant adjustments. Data analysis may trigger immediate actions while simultaneously influencing how future data is collected and communicated, creating a dynamic, interconnected process rather than a straightforward sequence.
One of the hardest parts of implementing an IoT remote monitoring system is integration. Read more about this challenge and ways we overcome it.
Collect data
Deploy sensors and devices on-site to monitor key parameters (e.g., temperature, pressure, machine performance, etc.).
Sensors gather real-time data and relay it to a local control unit or directly to the cloud.
Ensure data is collected at regular intervals to capture ongoing performance and any anomalies.
In greenfield scenarios, you will need to install sensors on your equipment to measure the appropriate aspects, whether vibration, flow, tank levels, temperature, speed, etc.
For brownfield operations, you’ll need to collect data from existing sensors, historians, third-party applications, and any other data sources you have. Data collection, communication, and processing is a lot more complicated in these scenarios, but it isn’t impossible. (It’s actually where we excel if you don’t mind us tooting our own horn!)
Communicate data
Data from sensors is transmitted via wireless or wired communication protocols (e.g., Wi-Fi, cellular networks, Ethernet, etc.).
Use gateways or edge devices to aggregate and transmit this data to cloud-based platforms or local servers.
Ensure communication protocols are secure and reliable to prevent data loss or tampering.
Analyze data
Data is processed and analyzed through machine learning models, analytics engines, or rules-based systems.
The system flags any anomalies or patterns that indicate potential issues (e.g., a machine running outside of optimal ranges).
Historical data is compared with real-time data to identify trends, forecast issues, or improve performance.
If you want to delve into more complex insights, such as trends, you’ll have to delve into intricate multivariable issues, combining factors like temperature, voltage, and speed. Uncovering trends in order to enable advanced solutions, such as predictive maintenance or automation, often requires extensive historical data spanning weeks, months, or even years to generate reliable results.
Visualize data
The analyzed data is transformed into user-friendly formats such as graphs, dashboards, and reports.
Dashboards are customizable to show KPIs, system health, and real-time alerts.
Remote teams and operators access the visualizations via web or mobile applications to monitor the system's status.
Predefined dashboards and KPI templates reflect your asset performance and can even give you control over your equipment and processes from anywhere in the world. Raw data, or even insights, without a user-friendly interface on which to view and understand it helps no one.
Act based on data
Operators receive actionable insights, condition-based alerts, or recommended actions based on the analyzed data (e.g., "perform maintenance on machine X").
Automated systems may trigger actions directly, such as shutting down equipment if critical thresholds are exceeded.
Teams can make informed decisions on-site or remotely to optimize performance, prevent downtime, or initiate repairs.
In Conclusion
Some industrial remote monitoring solutions are quite straightforward to implement, providing real-world business results in a matter of weeks. Others are quite messy, requiring the right team of experts to implement and integrate.
Are you looking for improved operations ROI, optimized performance, no unnecessary equipment downtime, and lower costs? Contact us for a free infrastructure assessment.