The Environmental Cost of Missing Wastewater Treatment Crises
Every day, 2 million tons of sewage, industrial, and agricultural waste is released into water worldwide.
In 2021, the Berkeley County Public Service Sewer District in West Virginia exceeded pollution limits 1300 times and allowed sanitary sewer overflow into clean water over 500 times. They were fined $518,400 by the EPA and required to implement improvements to their system, but the damage was done.
King County, home to Seattle, let stormwater mixed with wastewater spill into Puget Sound and was fined $361,000 for it.
This factory-made wastewater pollution is 100% preventable.
No One Wants Industrial Water Pollution
Most companies understand the serious consequences of wastewater spills and work hard to prevent them. However, despite their best efforts, spills can still occur due to a failure in equipment or a misstep in the process. When this happens, the environment is impacted and the company is faced with a significant financial burden.
A wastewater spill can result in hefty fines from regulatory agencies like the EPA, as well as the cost of clean-up and restoration efforts. These expenses can add up quickly. However, the damage to the company's reputation and public image can be even more devastating.
That's why it's so important for companies to have measures in place to prevent spills from happening in the first place. This can include regular maintenance of equipment, frequent check-ins on processes, and adopting effective solutions to catch any issues before they become bigger problems.
By taking responsibility for their impact on the environment, companies can not only avoid negative consequences but also demonstrate their commitment to sustainability and corporate responsibility.
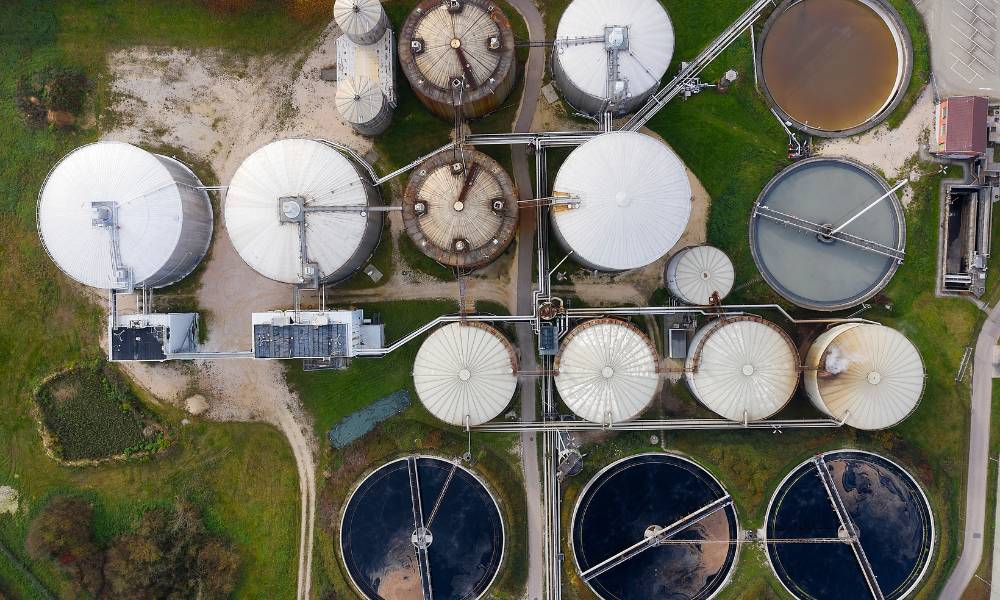
Remote Monitoring: Empowering Industries to Limit Wastewater Pollution
The good news is that there is a way to prevent industrial water pollution. IoT-powered remote monitoring technology provides a solution for industrial companies to prevent their wastewater from contaminating the environment due to equipment or process failure. With remote monitoring, companies can keep a constant watch on their wastewater treatment plants and detect any potential issues that would lead to sewage contamination in near-real-time or real-time. This means they can catch leaks, spills, or equipment failures as soon as they occur and take immediate action to correct them.
This technology uses sensors and monitoring devices placed throughout the wastewater treatment plant at key positions to collect data and provide real-time insights into the plant's performance. The data is then transmitted to a central system where it can be analyzed and used to identify any issues that may arise in near-real-time. This technology can even alert the relevant parties if any problems are detected so that action can be taken promptly.
Remote monitoring provides a level of visibility that was not previously possible. With real-time or near-real-time data, companies can be proactive in preventing contamination rather than reactive in cleaning it up after the fact. This helps reduce industrial water pollution's impact on the environment and protects our water systems from the damaging effects of introduced sewage and other waste products.
How Do Most Companies Currently Prevent the Risk of Sewage Contamination?
Too many companies still depend on manual equipment, plants, and process checks. However, these companies too often find manual monitoring to be:
Time-consuming: Checking equipment and processes manually is time-consuming, especially if done regularly, as it should be. This can take away time from other important tasks and reduce overall efficiency.
Error-prone: Manual monitoring is prone to unintended error. It can be easy to miss minute changes or other nuanced details or misinterpret readings, leading to incorrect decisions.
Inefficient: Manually checking equipment and processes can be a repetitive and monotonous task. This can lead to decreased attention and decreased efficiency over time, which can result in missed readings or errors.
Labor-intensive: Monitoring equipment and processes manually can be physically demanding, especially if done for long periods. This can result in worker fatigue and decreased productivity.
High costs: Hiring and training workers to perform manual monitoring can be expensive, especially if it needs to be done on a large scale. Manual monitoring becomes even more expensive when it prevents workers from participating in other crucial tasks, consuming their time unnecessarily.
Alarm systems are often set up to alert personnel of any issues. While this method gives a boost to manual monitoring, it's still limited by the human response time, which can result in substantial environmental damage before the issue is found out and addressed. We had the opportunity to implement a remote monitoring solution for a plant whose wastewater treatment plant was physically located in a far-away corner of the plant (as you’d imagine sewage would be). People just weren’t around that area frequently enough to hear the alarm when a crisis had happened.
On the other hand, remote monitoring uses advanced technology such as industrial IoT to monitor wastewater treatment plants in real-time or near-real-time continuously. This solution provides immediate visibility into plant operations and allows companies to quickly identify and resolve any issues.
.jpg)
Here’s how remote wastewater monitoring addresses the previous monitoring drawbacks to prevent industrial water pollution:
Less Time-consuming: Reduces the time required to manage assets by automating the monitoring process. Sensors continuously collect data and transmit it to a central system, reducing the need for manual checks. This frees up time for workers to focus on other important tasks.
Less Error-prone: Helps reduce human errors by automating data collection and analysis. The system can be set up to detect even minute changes in asset conditions and notify workers of any potential issues, which helps to avoid misinterpretation of data.
More efficient: Improves efficiency by providing real-time data and alerts to workers, allowing them to address any issues quickly. This reduces the need for repetitive and monotonous manual checks, leading to increased worker attention and efficiency.
Less Labor-intensive: Reduces the physical demands of monitoring assets by automating the process. Workers can remotely access data from a central system, eliminating the need to physically inspect assets on-site. This can also reduce the risk of worker fatigue and improve overall productivity.
Lower costs: While upfront costs may be associated with installing sensors and setting up a remote monitoring system, it will ultimately be more cost-effective than traditional manual monitoring. By reducing the need for manual labor, remote monitoring leads to lower labor costs over time. Additionally, remote monitoring can help prevent asset failures, which can result in costly downtime and repairs.
Overall, remote monitoring can improve asset monitoring by increasing efficiency, reducing errors, and decreasing labor costs, ultimately leading to improved productivity and reduced downtime.
Leading the Way in Environmental Stewardship
The problem of industrial water pollution affects us all. It is time for action. Remote monitoring technology offers a solution that is not only effective but cost-saving as well. Companies in industries with wastewater treatment plants can play their part in limiting environmental wastewater pollution by adopting remote monitoring solutions.
The future is bright, with the possibility of widespread implementation of prevention technology leading to a cleaner, healthier environment for all.