Analyzing the problem
Our client was dealing with a big headache—tools getting lost, stolen, or damaged during maintenance and outage projects at sites all over the world. These tools are essential for technicians handling high-stakes repairs, so every delay in finding or replacing them meant project slowdowns and costly penalties. It was adding up to over a million dollars in losses each year.
Here were their main pains:
Tracking solutions provided by vendors were insufficient, as they lacked the precision and functionality to meet the company’s unique needs.
Employees were reluctant to use existing mobile apps due to data privacy concerns, resulting in incomplete adoption of the tool tracking system.
The current solution couldn’t integrate data from multiple tool vendors or expand to meet broader needs beyond asset tracking.
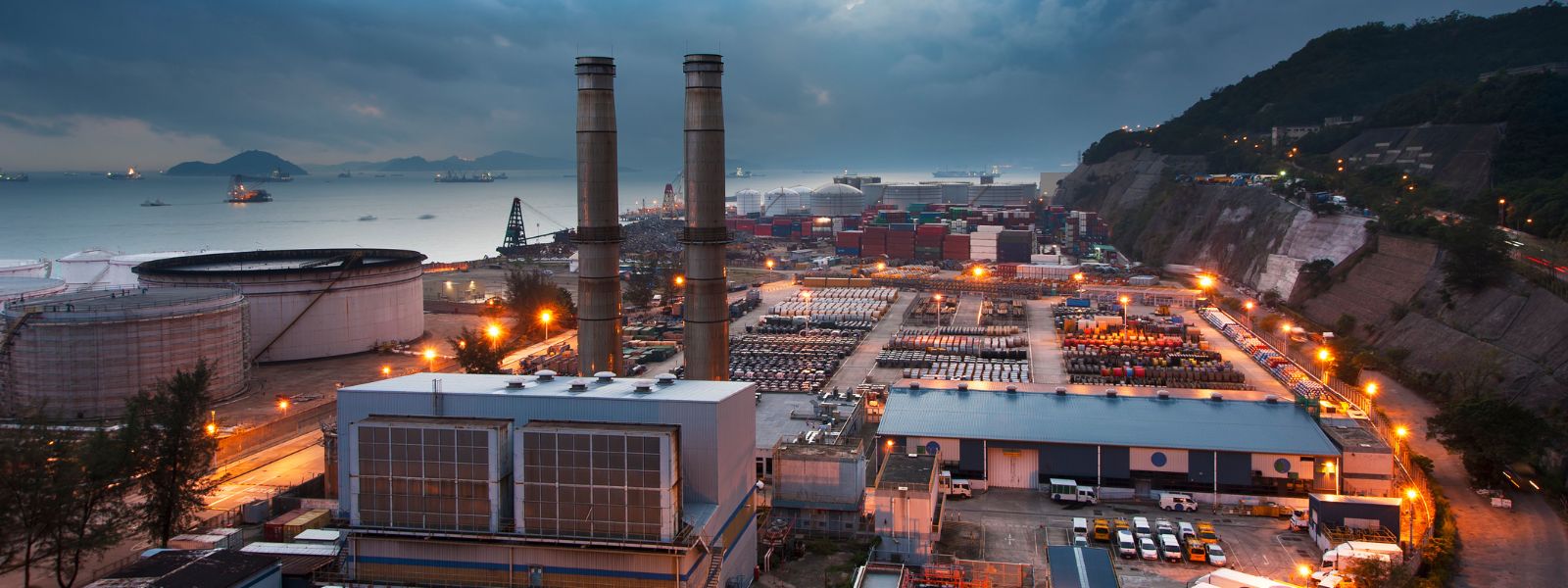
Implementing the solution
To tackle the challenge head-on, they teamed up with us to create a fully customized asset tracking system—built to boost efficiency, cut costs, and keep projects running smoothly. With Timbergrove handling everything from consulting to development and integration, we were able to deliver the solution fast and hassle-free.
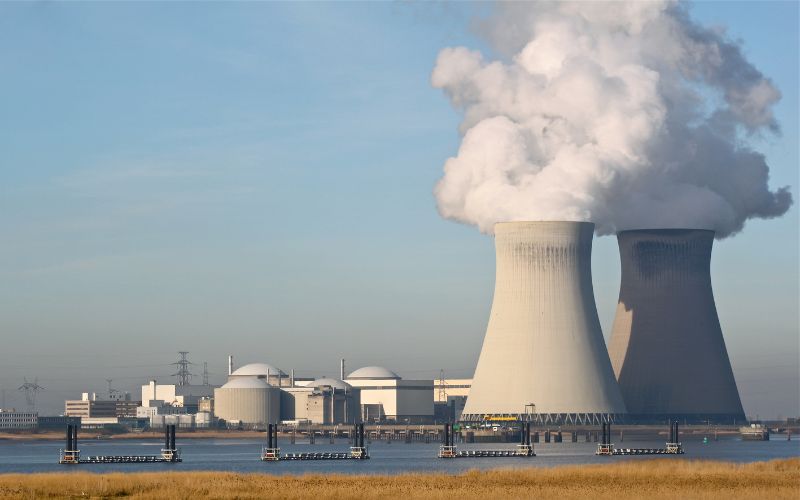
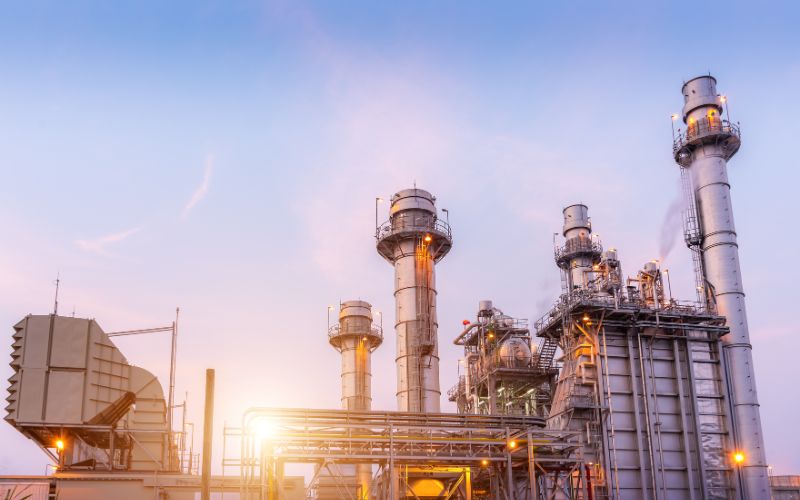
Results
A pilot implementation proved the solution’s ability to deliver significant operational improvements, paving the way for broader adoption and long-term scalability.
Cost Savings
Reduced tool misplacement helped the client drastically mitigate their losses.
Less Down Time
Delays caused by misplaced tools were eliminated, keeping projects on schedule and avoiding costly penalties.
Enhanced Efficiency
The use of existing rugged tablets maximized usability, minimized new hardware costs, and alleviated worker privacy concerns.
Future-Ready Design
The scalable platform ensures easy integration with enterprise systems, preparing the company for future operational needs.