Exploring Smart Factory Use Cases Powered by IIoT
In the digital age, industrial IoT (IIoT) is not just about connecting machines—it's the powerhouse behind transformative smart factory use cases. From predictive maintenance and remote monitoring to near-real-time data-driven decisions and seamless inventory management, IIoT-based systems are revolutionizing our manufacturing landscapes.
And the best part? Implementing these cutting-edge smart factory use cases is now more straightforward and cost-effective than ever. Dive in to explore the tangible benefits and visionary applications of IIoT in the modern factory setting.
Use Case 1: Predictive Maintenance
While the concept of predictive maintenance might sound like a plot from a futuristic sci-fi novel to some, it's a tangible reality in the world of smart factory use cases.
At its core, predictive maintenance leverages data analysis and machine learning, drawn from a network of sensors and intelligent edge devices, to monitor equipment and processes, pinpointing potential issues before they even arise. By continuously gathering and analyzing data, maintenance teams can spot patterns and trends, effectively predicting when a piece of equipment might hit a snag.
How does predictive maintenance work?
Through IIoT, assets, equipment, and machinery are embedded with sensors that gather real-time data. This continuous flow of information enables the early detection of any deviation from the norm.
The outcome? A notable boost in productivity, minimized unplanned downtimes, and an enhanced bottom line for businesses. So, while predictive maintenance might not be 'magical', its implications for businesses are nothing short of extraordinary. The U.S. Department of Energy supports this perspective, revealing that the deployment of predictive maintenance can offer an ROI that's up to 10 times the initial outlay.
Real Predictive Maintenance Scenarios
In hospitals, predictive maintenance ensures critical devices, from imaging equipment to ventilators, operate optimally, scheduling timely maintenance to prioritize patient care. Meanwhile, manufacturing plants utilize technologies like infrared imaging and vibration sensors to preemptively identify and address potential machine failures, mitigating costly downtimes.
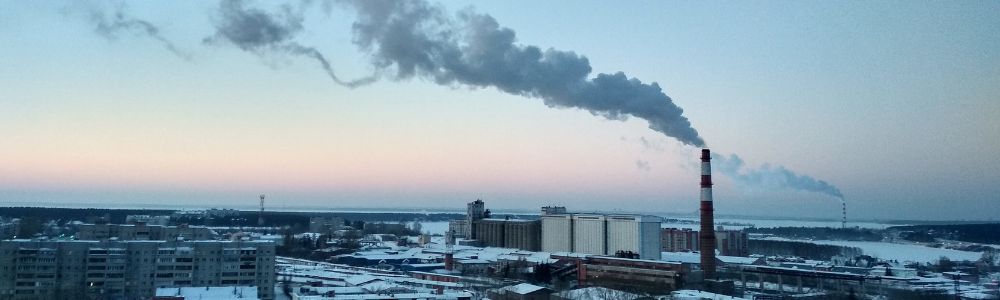
Use Case 2: Conditions-Based Monitoring & Alerts
Any factory owner knows that massive disruptions and downtime don't just halt production; they punch a big hole in revenues. Every moment equipment stands still or you're scrambling to address equipment failures, the financial losses accumulate. Enter conditions-based monitoring, one of the standout smart factory use cases, promising a smarter approach to prevent these sizable disruptions.
Sensors—customized based on your machinery and its operational variables—constantly keep an eye on equipment, promptly alerting you via instant notifications to any deviations from the norm. This isn’t about a simple heads-up; it’s about giving you ample time to respond before a tiny hiccup evolves into a major headache.
How Conditions-Based Alerts Work
Condition-based alerts operate on the principle of monitoring equipment or system parameters in near-real-time and triggering notifications when deviations from predefined thresholds or conditions are detected.
It comes with huge benefits to the workforce as well: fewer on-site checks mean lower labor costs and an inherently safer working environment, minimizing the risk of accidents. It's a winning scenario on all fronts, ensuring a smoother, more efficient, and financially savvy production line.
An Example of Conditions-Based Alerts Working
IoT-powered remote monitoring technology enables industrial companies to prevent wastewater contamination by continuously overseeing their treatment plants in real-time. Using sensors placed at key positions within the plant, this system collects data and promptly alerts relevant parties of any leaks, spills, or equipment failures. This proactive approach reduces the environmental impact of industrial water pollution and ensures timely intervention before significant damage occurs.
Use Case 3: Asset Tracking
Imagine this: from the moment raw materials enter your factory, to the moment your finished products are deployed across the globe, everything is under your watchful eye. With IIoT-powered asset tracking, businesses integrate sensors and connected devices to offer an unparalleled birds-eye view of their assets throughout their entire lifecycle.
How Asset Tracking Works
It's more than just a "Where is it?" service. Real-time data about asset location, movement, and critical operating parameters like temperature, pressure, and vibration can be collected and analyzed. This isn't merely about keeping tabs on items; it's about having more control over every facet of operations, ensuring that key equipment and processes remain within defined boundaries, all while optimizing your financial and operational performance.
On top of that, the real value comes from what you do with that information. Beyond just locating assets, the real value springs from understanding their condition, utilization rate, and performance. Financially, such keen insight allows businesses to pinpoint underutilized assets and optimize their balance sheets, making informed decisions about repairs, relocations, or removals.
Asset Tracking in Real Life
Operationally, the continuous stream of data becomes a proactive tool. Take, for example, an agribusiness tracking a critical shipment. A sensor within the shipment doesn't just provide location updates—it can alert personnel if temperatures rise beyond acceptable levels or if the shipment experiences excessive force.
And from a commercial perspective, real-time monitoring means maintenance no longer operates on guesswork. A rise in energy use or an abnormal pressure reading? These are clear signs that maintenance intervention is required. So, the next time someone asks why asset tracking is all the rage in smart factories, you can confidently say it's about having more control and driving operational excellence.
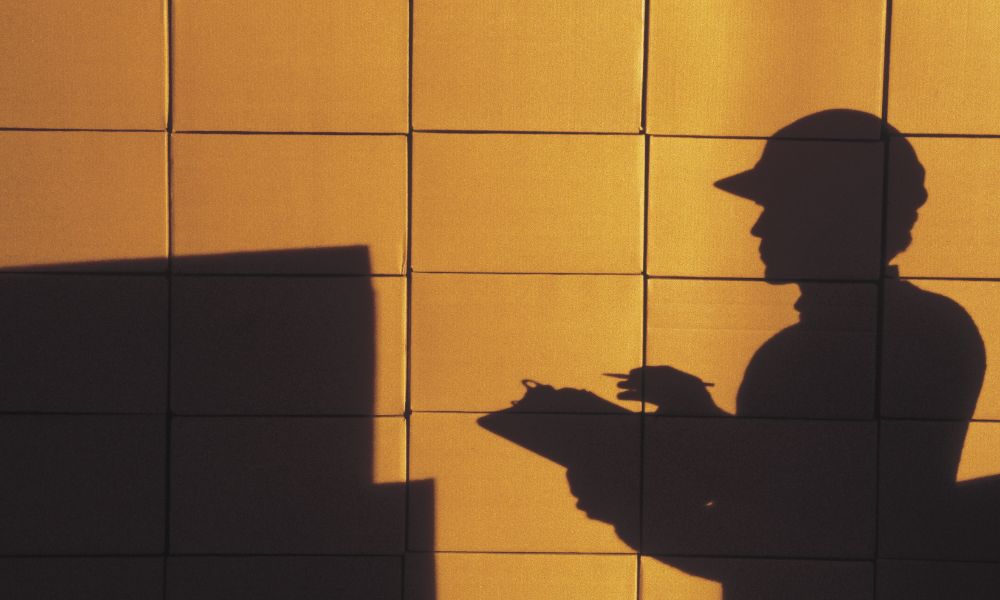
Use Case 4: Inventory Management
Now let’s look at inventory management as one of the less flashy, but seriously advantageous smart factory use cases. Having more control over the whereabouts, condition, and availability of inventory items not only streamlines operations but also empowers companies to make smarter business decisions. When businesses can seamlessly track raw materials, finished products, and even spare parts with pinpoint accuracy, they open doors to greater resource allocation, waste reduction, and financial savings.
How IIoT-Powered Inventory Management Works
Each inventory item can be tagged with an RFID chip, which contains unique encoded data about that particular item. These tags are scanned by RFID readers, which then send this data, along with their location and timestamp, to a cloud-based system. This cloud system processes the data, determines the location of each inventory item, and offers real-time visual updates.
What this means for businesses is the ability to monitor their inventory, whether it be in a sprawling warehouse or a compact retail space, using just a smartphone or laptop, no matter where they are.
Examples of Inventory Management
Let's take the scenario of a manufacturing plant that produces automobile parts. Every component, from tiny bolts to large engine blocks, is crucial in the assembly process. Here's where smart factory use cases, especially IoT-driven inventory management, come to the rescue. With RFID tags attached to every batch of raw materials or parts bins, the manufacturing facility can monitor the consumption rate of these materials in near-real-time. As the assembly line utilizes these components, the RFID system can automatically detect low stock levels, alerting the procurement team to order more or the production team to adjust the manufacturing pace.
Use Case 5: Industrial Process Automation
Industrial automation, supercharged by the growth of IoT, presents businesses with the golden opportunity to streamline operations, minimize manual intervention, and thereby elevate performance levels. This isn't just about cutting-edge tech—it's about ensuring processes are optimized, costs are reduced, and decisions are data-driven.
How Automation Works
At its core, industrial process automation is about transforming data into actionable insights. Here's the sequence: sensors and IoT devices, spread across various points in a manufacturing process, continuously collect real-time data. This data is channeled to a centralized system, which, powered by advanced analytics and machine learning algorithms, identifies patterns, forecasts equipment failures, and pinpoints potential production bottlenecks. The beauty lies in its proactive nature; instead of reacting to issues, the system automatically optimizes operations based on the insights derived from the data. Whether it's a sensor identifying a dip in machine efficiency or algorithms scheduling preventive maintenance, the emphasis is on minimizing disruptions and maximizing equipment longevity.
What Automation Looks Like in the Wild
In the textile manufacturing industry, a sector where consistency and quality directly influence brand reputation, industrial process automation serves as a linchpin for success. Advanced looms and weaving machines, integrated with IoT sensors, can continuously monitor the tension and quality of yarn, ensuring that the fabric produced meets stringent standards. Should a sensor detect an inconsistency, like a snapped yarn or a misweave, the system can immediately pause the loom and alert an operator, preventing wastage and ensuring top-notch quality.
The ROI of These Smart Factory Use Cases
Embracing the digital transformation brought by these five smart factory use cases presents a genuine investment in the future. Between the significant reduction in operational costs and the marked enhancement in production efficiency, these systems quickly justify their initial setup costs.
Indeed, when considering the long-term positive ROI, it becomes evident that smart factory use cases aren't just trends—they're strategic shifts that empower businesses to thrive in an increasingly competitive landscape.