The Internet of Things (IoT) revolution emerged around the turn of the century, first coined by Kevin Ashton as part of an RFID tracking project. Today IoT accounts for around $40 billion of market value, with roughly a quarter of businesses using IoT products. Asset-heavy industries such as oil and gas have particularly profited from the IoT boom.
How? There are many benefits to implementing industrial IoT in the oil and gas industry, including real-time monitoring, automation of manual tasks, and compliance with regulatory standards. Ultimately, oil and gas companies can expect an extremely positive ROI after the initial investment, thanks to a combination of reduced downtime, prevention of production loss, and increased productivity.
Here are some of those IoT use cases and their benefits:
Extend the lifespan of your upstream OEM equipment. I.E. Drawworks and Top Drive systems
Detect anomalies for upstream operations, effectively and at scale
Detect hazardous gasses before major events occur
Monitor storage tank levels to prevent spills and leaks
1. Extend the lifespan of your upstream OEM equipment. I.E. Drawworks and Top Drive systems
A lot of systems in the oil & gas industry, such as the drawworks control system or top drive system, are Original Equipment Manufacturer (OEM) systems. These predominantly proprietary systems offer operators a limited access to their control networks. Which means most of these systems don’t provide access to the kind of data you would need for maintenance or performance optimization purposes, especially for predictive maintenance.
However, by installing additional sensors, such as vibration, temperature, speed, weight, and pressure sensors, directly onto the mechanical parts of your drawworks or your top drive systems, operators can gather more comprehensive data. By combining this data with the existing system data, and using machine learning, operators can identify patterns and events that lead to increased wear and tear and potentially equipment failure. With this knowledge, operators can implement predictive maintenance measures to reduce the risk of machine failure.
As long as you don’t interfere with its operation, existing sensors, control systems or control network, you can usually add additional sensors, even wirelessly, to existing equipment, even if it’s OEM equipment.
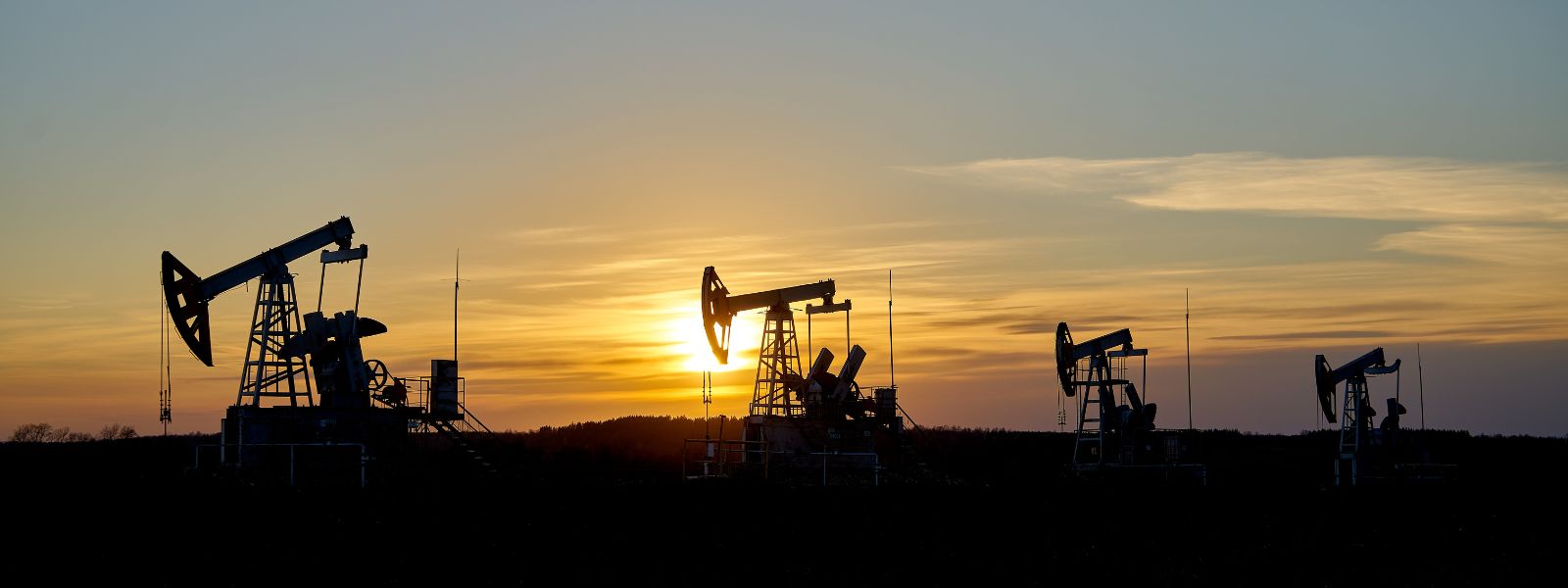
2. Detect anomalies for upstream operations, effectively and at scale
Monitoring low-productivity wells is a major challenge in upstream production and provides a great opportunity for internet of things in the oil and gas industry. The usual methods of using Programmable Logic Controllers (PLCs) and Supervisory Control and Data Acquisition (SCADA) systems for remote monitoring are not financially viable for low-productivity wells as these systems are expensive, with each part costing thousands of dollars. And those wells just don't generate much profit.
Why remote monitoring with IoT is more effective and efficient
IoT-powered remote monitoring eliminates the need for both physical visits and individual well-checks, allowing operators to remotely collect near-real-time data from multiple wells simultaneously without any trips to the well.
You see, we’re able to go a step further than remote access by setting up specific thresholds and alarms—essentially real-time monitoring at scale. Operators receive immediate notifications when there are deviations in production parameters which means they don’t need to constantly have eyes on the their wells. This enables them to take prompt action and make necessary adjustments to optimize resources at multiple wells at once. By adopting this proactive approach, potential issues can be identified early on, preventing them from turning into expensive complications. Ultimately, this ensures the seamless operation of upstream production activities.
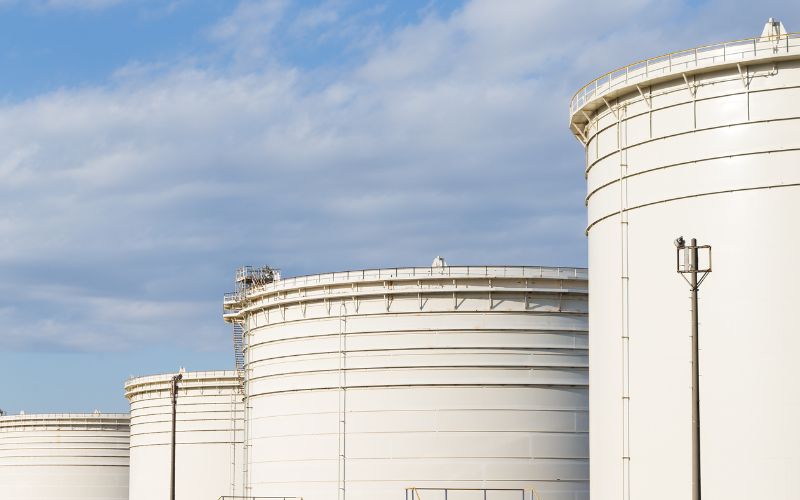
3. Detect hazardous gasses before major events occur
In remote locations with limited local monitoring, there is a genuine risk of dangerous gasses spreading and causing harm. However, by installing gas sensors that can quickly detect the presence of these gasses and raise alerts, proactive measures can be taken to prevent a more severe incident from happening.
Gas detection & condition-based alerts
By deploying advanced gas sensors strategically throughout the site, the system can continuously monitor the air for the presence of harmful gasses. As soon as any of these gasses exceed a predefined safety threshold, the system triggers immediate alerts or work orders to the designated personnel. This notification ensures that swift action can be taken to mitigate the risk.
Upon receiving the alert, trained personnel equipped with proper safety gear can quickly respond to the site for inspection and necessary actions. By promptly addressing the gas release, they can prevent the spread of the hazardous gases, safeguarding the well site, workers, and surrounding areas from potential harm.
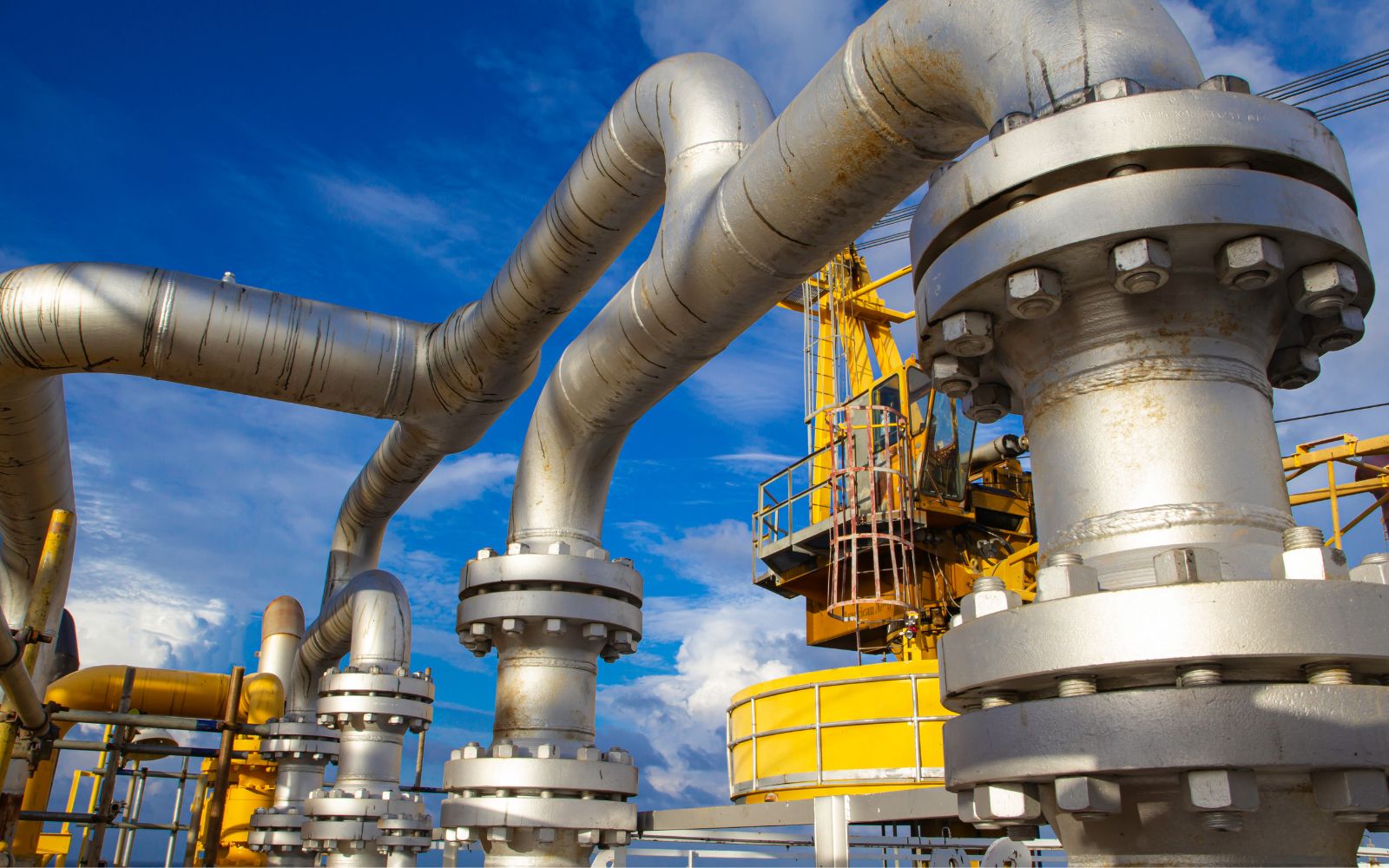
4. Prevent spills and leaks
In upstream operations, dealing with the extraction of oil and gas at the same time brings its own difficulties. One particular challenge is the potential when storage tanks used to contain oil from production wells reach their upper limits. Without constant monitoring, these tanks can overflow, resulting in oil spilling onto the ground. The consequences of such spills can be significant and must be addressed promptly.
Monitor tank levels constantly
To tackle these issues and prevent potential environmental hazards, the implementation of IoT technology proves invaluable. By installing sensors that monitor tank levels and detect the presence of harmful gasses in the surrounding area, operators can gain real-time or near-real-time access to critical information. By using remote monitoring, events can be quickly identified, allowing for timely intervention.
Continuous monitoring of suction rod pump stuffing boxes
Another cause of oil spills is when the stuffing box in a sucker rod pump starts to leak, or worse, when there is a leak in a pipe or valve. By installing monitoring IoT sensors that use thermal and vision sensors, the spill can be detected as soon as it occurs, notifying the operator or even shutting down the pump.
Ready to implement monitoring at your site?
Get IoT-based monitoring up and running sooner and for less than you think.
Get startedThe ROI of Implementing IoT in the Oil and Gas Industry
If you ask the average person working in an industrial field how expensive IoT is, they’d probably answer that it’s high. While costs have decreased significantly in recent years, thanks to out-of-the-box solutions, the investment remains a significant factor in the decision to implement one of the use cases mentioned above, not because of the value of an individual device, but because of the scale of oil and gas operations.
However, the ROI of those same investments almost always overshadows any original investment, in our experience. By using IoT technology, oil and gas companies can streamline their operations, reduce costs, and increase productivity—all of which provide positive ROI in the long term. Time and time again, the benefits vastly outweigh the detractions.
Sometimes the cost-effective solution is not off-the-shelf.
The oil and gas industry has specific and unique operational challenges for many reasons, such as the changing nature of operations, dealing with harmful and flammable fluids, and the scale of operations, to name a few. At Timbergrove, we have been helping industrial companies develop innovative products and solutions to cost-effectively solve their challenges for more than 14 years. We excel at understanding our customer's unique problems and developing an innovative solution, from concept design to hardware, embedded software, human interface development, and overall system implementation.
For personalized consultation on how you can reap the benefits of the internet of things in the oil and gas industry, let’s start a conversation.